降本增效(3)-设备利用率越高越好?
设备管理对于企业的生产运营至关重要。传统生产模式下对设备的管理方法侧重于最大化设备利用率,即长时间的生产过程中很少换型,通常导致大批量生产、过多的库存、糟糕的准时交付率。在精益生产环境下,设备管理方法需要进行改变,以下是传统设备管理方法和精益设备管理方法之间的对比:
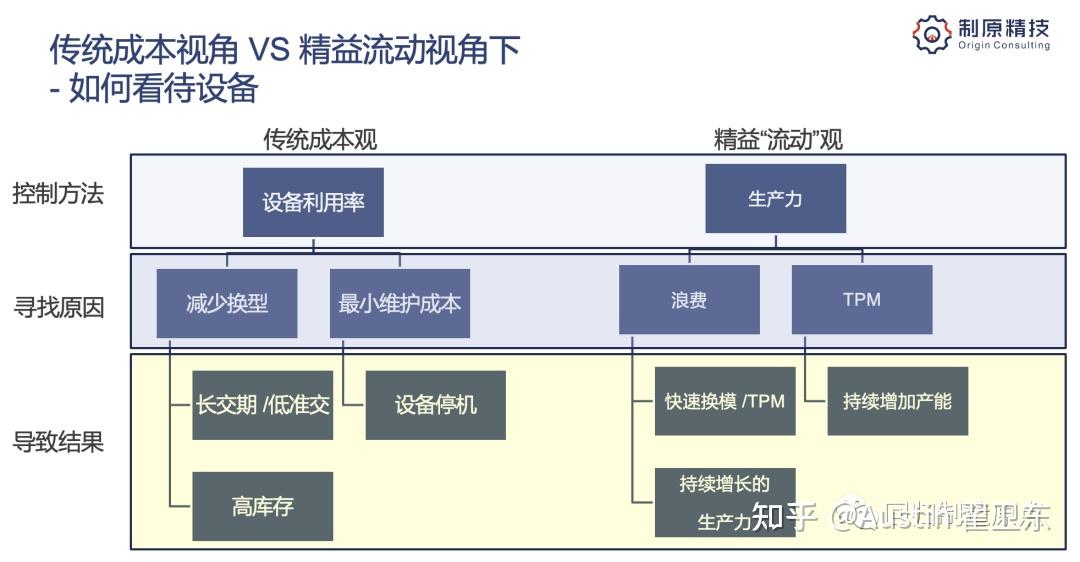
传统成本观的设备管理
- 最大化利用率:长时间的生产过程中很少换型,通常导致大批量生产和过多的库存。
- 以设备数量和设备利用率为主要衡量标准
- 复杂的工单系统:使用复杂的工单系统来跟踪每个作业(生产作业和维护作业)所花费的时间和物料。
精益的设备管理
- 提高生产力:精益企业关注的是整体流动的生产力而不是设备利用率(见上文)。
- 基于价值流会计的设备成本核算方法:价值流会计将实际的直接成本分配给价值流。所有支出都分配到费用产生地方。这样做可以使每个人都参与设备费用的分析。
- 实施全面预防性维护(TPM):全面预防性维护(TPM)可以最小化非计划停机时间,因为TPM是计划好的,所以不会破坏流程。
- 管理换型:为了提高机器生产效率,必须先稳定和标准化换型,然后再持续改善减少换型。
- 测量品质:在生产单元(尽可能建立机加工单元)和价值流中每天测量品质,这将改善流程并降低品质费用。
精益企业将设备视为资源,关注的是提高生产力。通过减少浪费,消除问题产生的根本原因,从而最大限度地提高设备产能。这种方法可以帮助企业最小化设备支出,提高生产力和增加利润。
共有 0 条评论