直面攻坚-表面处理行业的精益改善三部曲-1
和我们美好生活息息相关的表面处理行业(清洗,电镀,花絮镀等等)在现阶段产业转型升级过程中存在各种各样的痛点:
-良率损失 (比如清洗电镀良率波动85%~93%,大量返工报废,导致前面的注塑工序本来富余的产能成为瓶颈)
-设备利用率低下(OEE,TEEP)
-人力成本过高(大量的人工用来做上下挂的工作,以及大量人工做目视化检查)
-企业尝试推行自动化困难 (产品类型过多推行自动化困难,质量问题多无法导入视觉识别自动化)
-当然还有因为内部物流整体规划等难题(原材料,在制品,成品库存过高占用现金流,生产计划混乱)
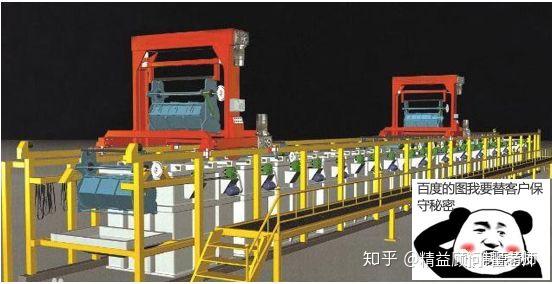
在做完价值流分析Value Steam Mapping,并且和工厂高层沟通期望后,我们认为首先要直面最难点-解决对方的工艺良率问题。因为如果不去解决最紧迫的良率问题,那么返工,人工过多,前工序产能瓶颈,生产计划不能达成等问题就是个死循环,简单的处理只能把问题表面覆盖住。
本案例实施过程:
第一阶段设备的稳定
要解决复杂工艺的良率问题,首要条件就是保证设备的稳定,设备稳定后可以排除大多数不相关(造成不良)的因子。我们需要对客户清洗线快速实施TPM设备全面维护的自主维护。
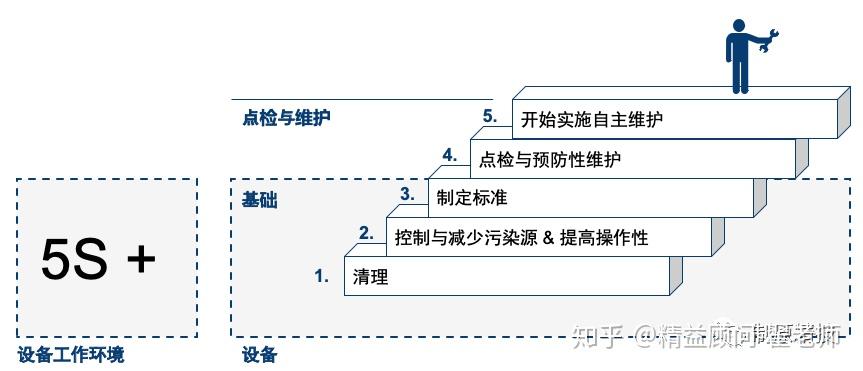
- Step1 对设备的彻底清洁,识别微缺陷建立快速改善行动清单
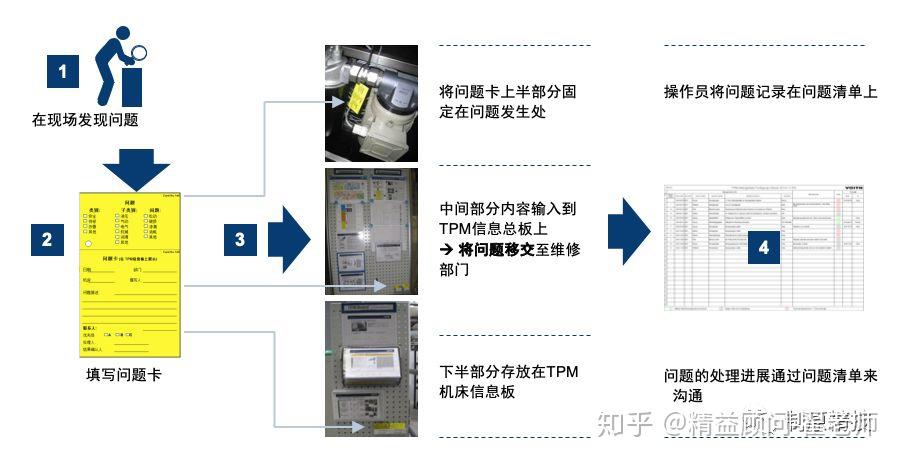
- Step2 减少和控制污染源,减少员工清洁和点检的时间
这里要每天对设备泄漏的地点进行拍照分析,彻底改善设备泄漏问题。并且对设备进行改造,让员工去点检的过程舒适,没有危险。
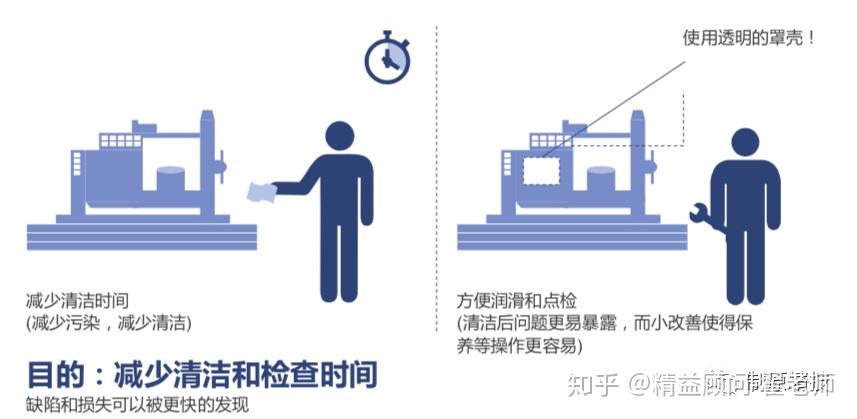
- Step3 定义设备的目视化标准
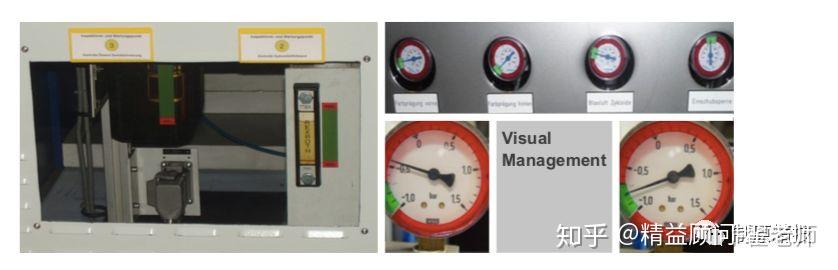
- Step4 培训点检与预防性维护
这里需要制定清洗设备的现场管理看板(包括人员架构,清洁计划,点检日历,OEE指标,维护手册,一点课程等)
- Step5 开始自主维护
这里有个重要的原则,在推行设备点检建立设备标准后,为了保证产出100%的良品需要对加工条件进行点检,需要深入探讨工艺的原理原则:
-工艺品质管理的关键因子
-基准
-数据采集的方法设备,采集周期
-异常的处理
(关系到客户工艺参数,这里不放图了哈)
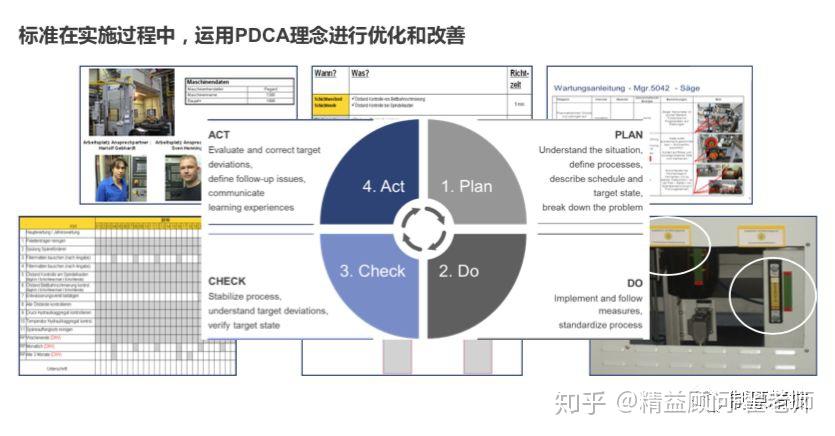
初步绩效
实施TPM后停机时间降为0,良率初步稳定(详见后文)
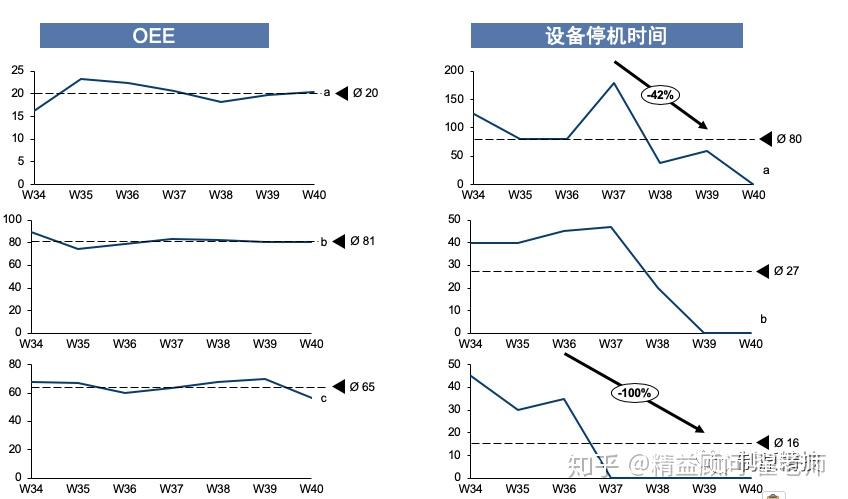
我们讲精益改善实施成功有两个重要的纬度,一个是实施的层级深度,一个是实施范围的广度。在面对表面处理这样复杂的问题时,我们需要对实施的深度进行评估:
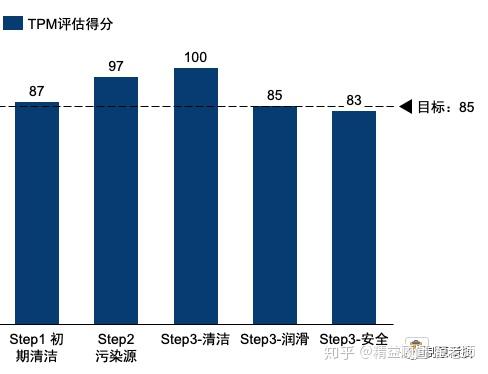
毫无疑问我们改善团队在这个TPM实施的过程中努力度
(未完待续......)
共有 0 条评论