5S-制原方法论
笔者在最近的几个精益项目中推行了数个5S研讨会,客户普遍反映超出预期:
- 极短时间内改善了生产现场(5天内),后续推广非常迅速有效(3周)
- 员工参与度很高,非常热情,学到了很多知识
- 爆破性绩效(生产效率提升20%)
- 方法结构化,适合集团性企业
对比其他5S的推行方法,制原5S方法有什么不同?
可以从方法论和实施层级这两个方面来阐述:
1.方法论:
- 方法论注重极简和系统化
前3个S是要求员工去做,强调口诀化。整理的3句口诀为:“1.区分要和不要;2.按频率分;3.单一最好”。(还有一句秘诀:“犹豫时已非必要”,)产线的员工可以短时间内立刻学会,还可以立即培训他人。
第4个S则利用非常详细的表单工具来建立标准。
前面4个S做好并且能长期坚持,那么第5个S就算是达成了,简单吧。
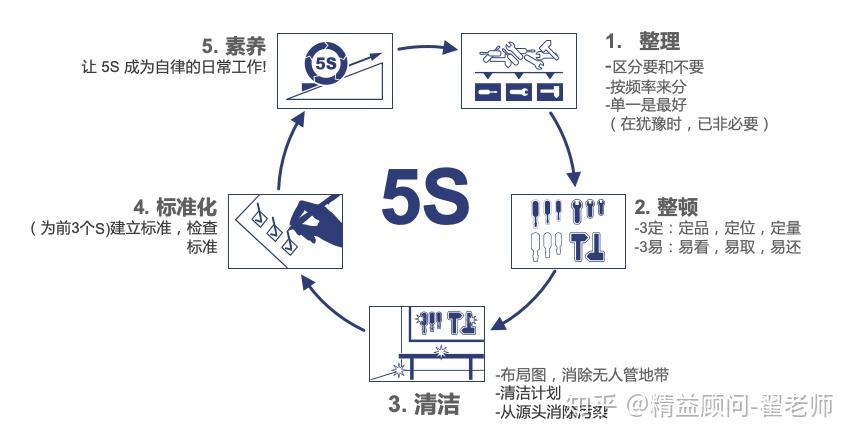
- 在样板区导入5S时,严格按照7步法实施:
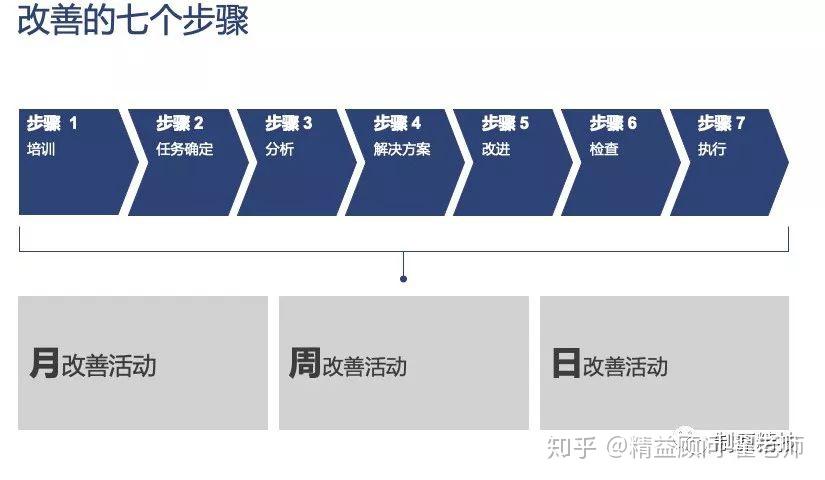
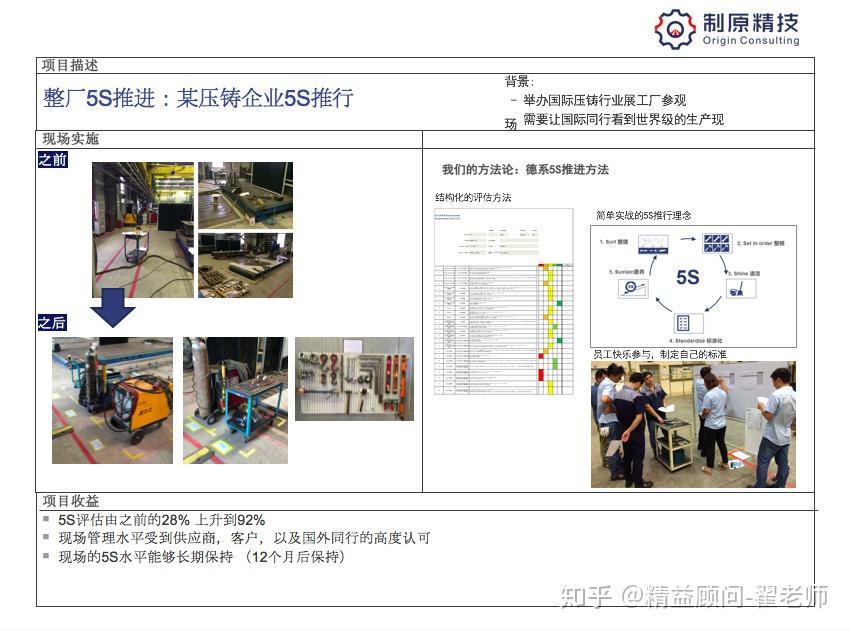
2. 实施层级
制原5S方法通过4个层级来现场和员工手把手实施
- Value Added Level增值层级
对整体布局的详细观察,通过消除8大浪费的方法设定完美布局。对每个工站的物料,工装,夹具,工具,以及员工的操作手法,从改善效率和良率的角度进行快速改善,并且用5S的方法设定标准固定下来。
- Material Level 物流层级
现场和员工探讨,对原材料,在制品和成品进行标准化。利用TOC的瓶颈理论观点快速设定在制品缓冲,提升产能。
- Information Level 信息层级
建立班组基本的管理看板,将班组层级需要管控的安全,班会,5S评估,布局图,清洁计划,多技能矩阵,PDCA流程固定下来。
- Management Level 管理层级
通常和SFM(车间现场管理Shop Floor Mangement)联系起来,对5S评估的指标进行标准化,要求现场班组长评估的分数和总经理评估得分一致。后续5S评估的指标和OPEX KPI BI系统相连接,通过数据指标把控集团各个现场的5S情况。
综上所述,制原的5S方法在快速导入,结构化推行,指标控制和团队持续改善上优势明显。如果您的企业有以下困扰,可以联系我们:
- 反复5S推行失败,不能维持
- 需要快速改善现场,取得爆破性绩效
- 需要集团推进的,KPI指标化的
- 需要快速培训大量基层人员的
共有 0 条评论