记一次组装生产线的快速改善
最近在一医疗器械工厂(轮椅)做组装部门改善,花2天时间把从车间混乱、人员散漫、效率低下的状态,改善成布局物流清晰、员工作业有节奏、班组长主动管理的状态,生产效率从之前的120台/每天到205台/每天。
组装部门改善前的背景:
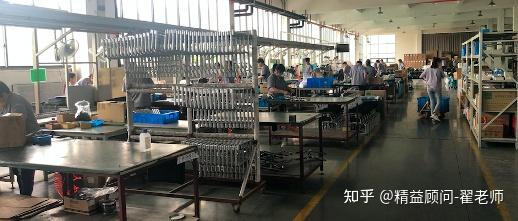
- 订单很多,员工每天加班3个小时,很多时候1周都没有1天休息
- 员工考核按照加班工资,所以效率高的和效率低的员工一样收入水平,老员工纷纷离职
- 总装线只有一个老员工,还是个聋哑人
- 新上任组装管理者,处于蒙圈状态
- 产线的缺料问题之前已经改善完毕(仓库和采购的追料看板改善完成)
- 产线产品有很多切换,切换时间很长
- 新员工太多,还有很多临时工(工资低),效率和之前比每天都达不到目标
- 现场处于混乱状态,员工作业没有节奏,满眼都是走动、等待的浪费
也有好的地方:
- 有作业指导书,还有部分老员工
- 工厂高层非常关注和紧迫
一开始也蒙圈了,我都是呆外企的,没有见过这么崩溃的场面。
具体做法:
1.既然提到人的问题,就要直面问题
使用多技能表格和班组长分析人员多技能,发现他们把技能不足的临时工放总装,而总装效率受制于最慢的工站(瓶颈工站),立刻替换人员,要求每个人必须会自己前后的3个工作技能。
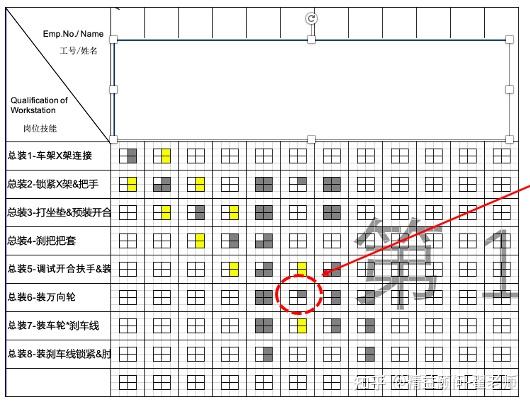
2.现场分开总装和子装配(后续还可能要合并,但是在混乱状态下首要任务是问题可视)
- 拆除妨碍总装员工的设施(桌子、多余的物料、无用的设备)
- 快速使用精益管和物料盒子改善每个工站,方便员工作业,减少员工寻找等待的动作浪费
- 使用精益管制作多台送料小车
- 总装缺料会拉动子装配的供应,迫使子装配跟上总装节奏
- 分开后谁快谁慢一眼就看的清清楚楚
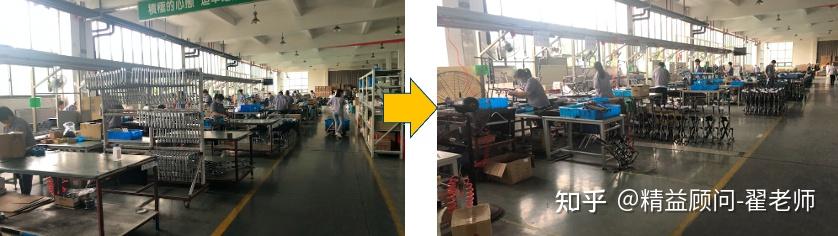
3.设立安灯制度
设立总装的工站牌,每个工站安装报警灯,总装的员工不允许离开工站,有异常要按灯报警。
- 班组长脱产,时刻处理异常
- 总装缺料时,和子装配班组长沟通及时补料
- 产线受阻时,和老师分析哪个动作可以减少合并(通过标准作业SOP)
- 员工要离开岗位时候补岗
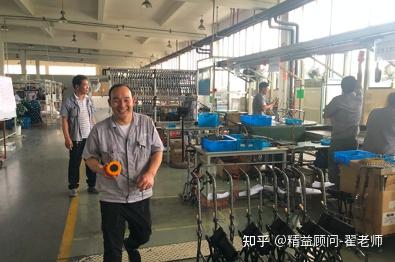
使用每小时产出看板来分析实际和目标的差异,说明原因,并且在下个小时解决这个问题
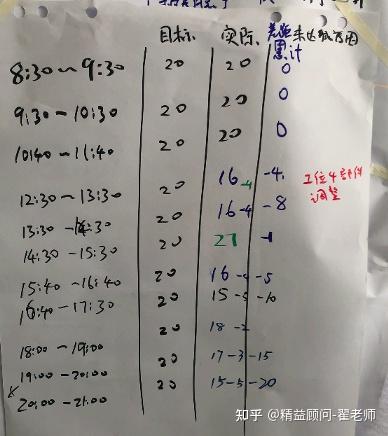
4. 其他后续的小改善
比如产线5S,物料切换的备料区(在两天内还没有完成)
5.关于人员绩效管理
后续要改变当前这种按加班给绩效的政策,明确按工时产出考核;在保证员工的收入下,减少加班。
个人心得:在一些管理混乱的组织(部门或者小区域),管理者需要充满勇气,努力面对这样的混乱情况,大喝一声,投入现场,动手去改善。很多人缺的不是方法和技术,而是和公司一致的目标,以及一马当先的勇气。
这次改善是在紧迫条件下为客户解决痛点问题,下面贴一下标准组装线改善的方法论。
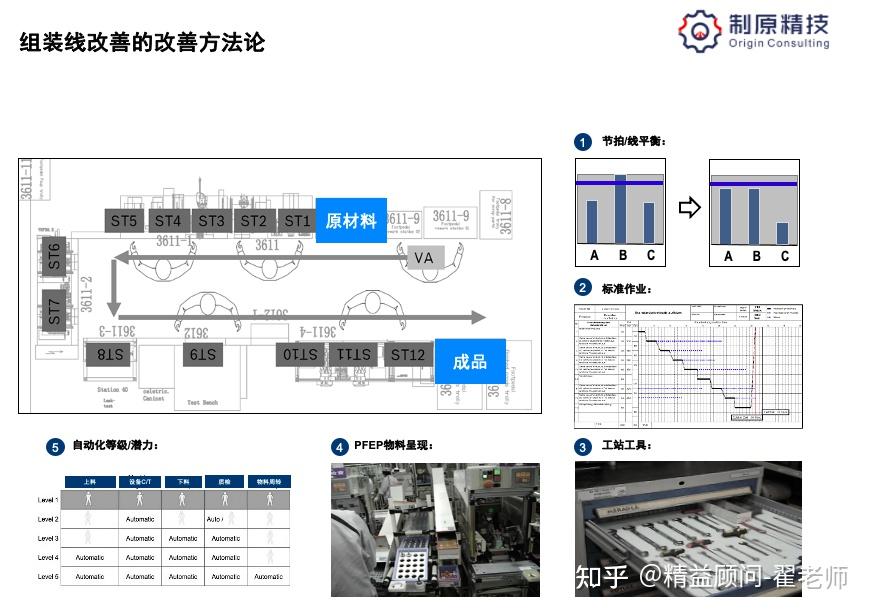
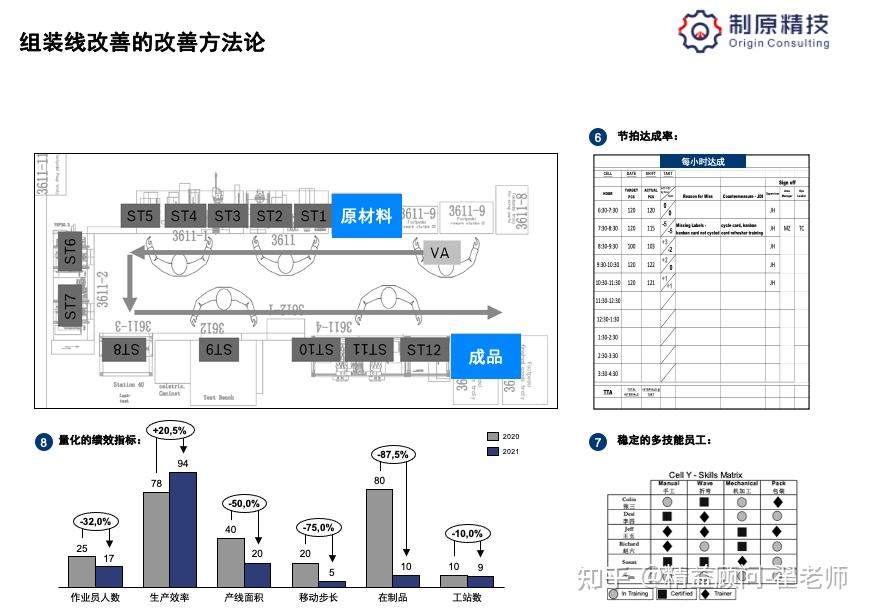
谢谢您的阅读
共有 0 条评论