将精益原则导入仓库
虽然精益原则和实践已在制造业中被广泛采用,但在过去几十年里,精益在仓库和配送中心环境中的运用相对来说是比较慢了。
与在制造现场的精益实践不同,在仓库中应用精益实践的目的,是为了加快物料的流动,消除浪费和减少库存。当然精益的原则和实践不会改变,在这里精益被用来转变仓库所特有的流程:收货、存放、储存、拣选和运输。
精益仓库的主指标:
KPIs | (超过3年) |
---|---|
生产力提升每年 | 4.96% to 8.13% |
拣选出错率下降(准确率基数99%+) | .004% to .09% |
库存准确率每年提升(准确率基数99.985%) | .0046% to .0078% |
安全(事故损失时间减少) | 2.5% to 5.65% |
仓库面积减少 | 8.55% to 14.65% |
案例数据来源:lean.org, Putting Lean Principles in the Warehouse
如何导入精益原则实施仓库转型?主要抓住以下3个方面:
1.客户导向,从跟随物料的流动出发
从传统仓库转型到精益仓库不是“一刀切”的活动,首先要思考我们的客户需要什么?通常在生产区域实施改善后(完美布局、一件流的生产线等),为了支持生产区域改善需要启动精益的补料方式,以此来拉动仓库改善。
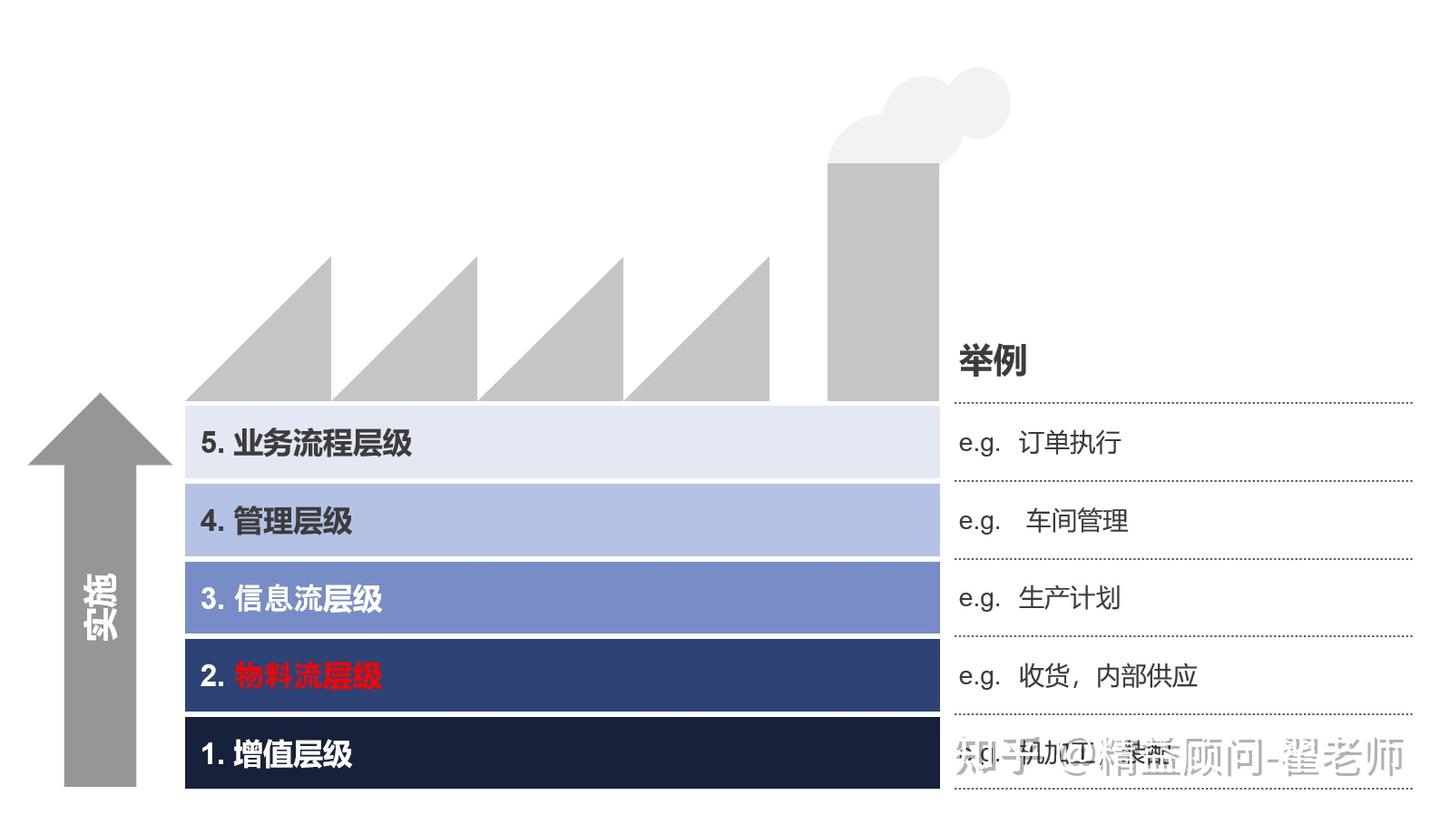
领导精益仓库转型的经理,需要通过价值流工具来识别浪费,并且为仓库中的零件设计完美的布局。
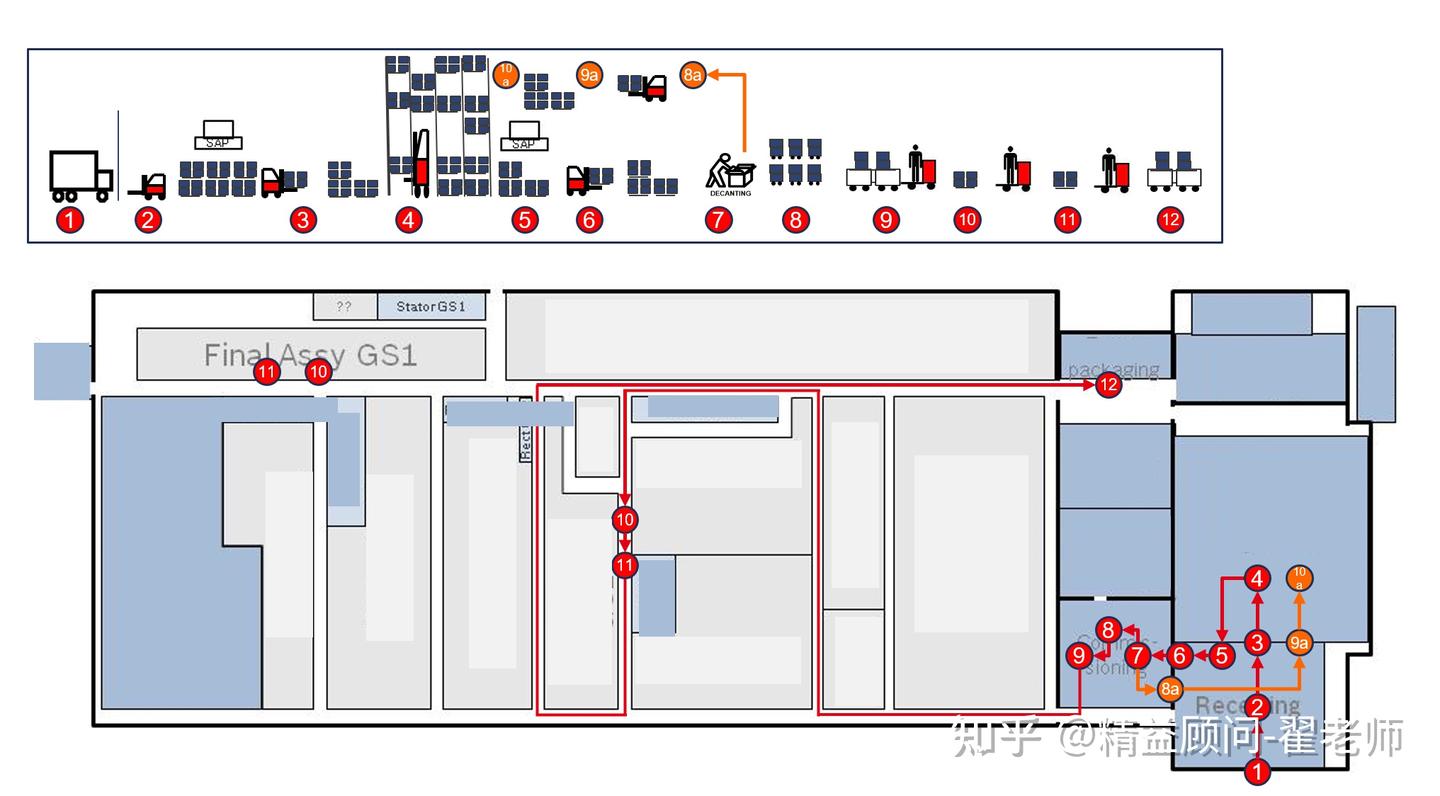
2.进行改善活动,重点是重新设计仓库流程
仓库精益转型中的KAIZEN活动与生产现场的KAIZEN基本相同,在生产现场的改善主要关注的是提高工序作业的效率,而仓库的改善是以提高物料流动的效率为目的。
仓库精益转型,可以通过以下工具来重新设计仓库的流程以优化物料流:
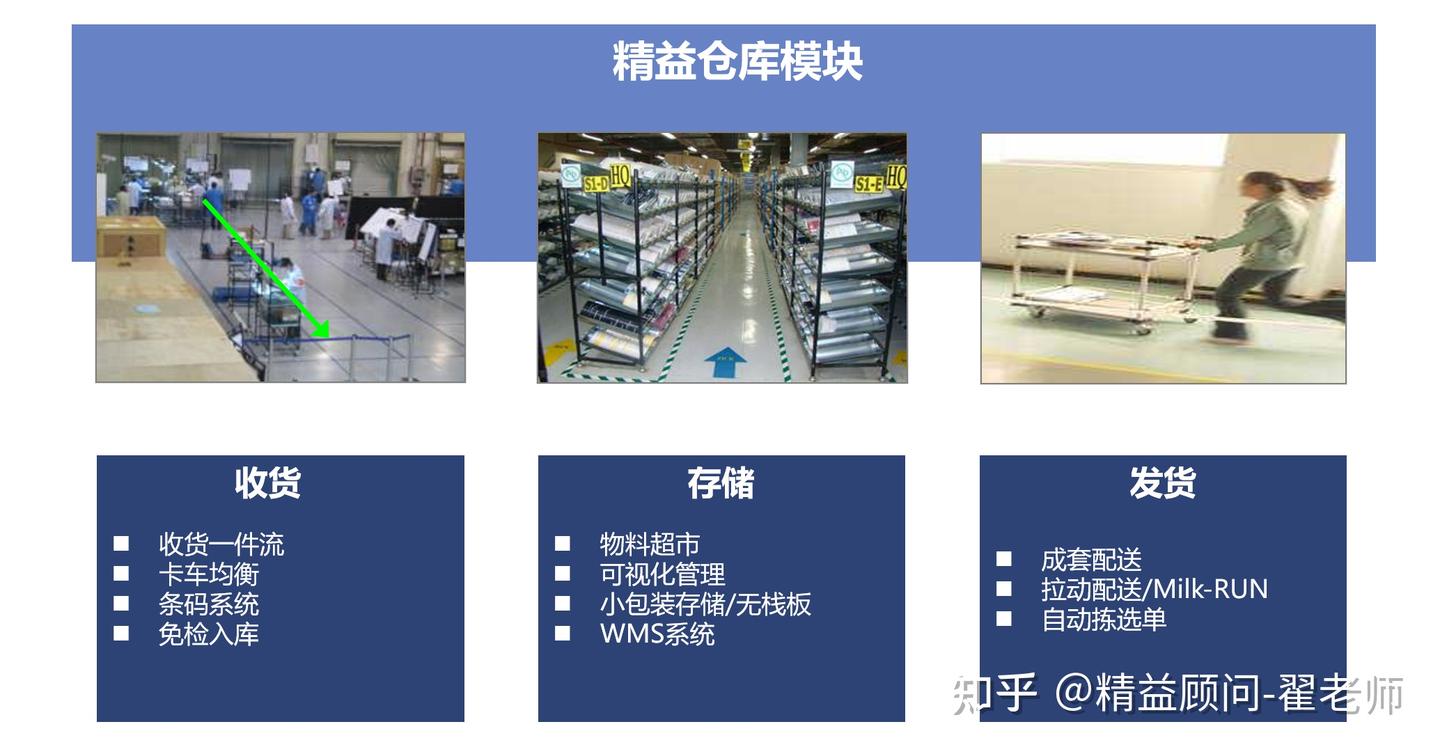
和任何精益转型一样,获得成功的关键要素之一是团队培训。首先要进行现场经理级别的培训,VSM、改善周、5S、和目视化管理。员工首先将进行价值流的练习,然后集思广益,看看哪里可以进行改进,以及那些流程的浪费可以快速被消除。然后接下来的6个月内需要把价值流识别的问题点按照优先顺序制定改善计划,并且每周确认结果。
采用结构化的改善周的模式有助于加速仓库的精益转型。
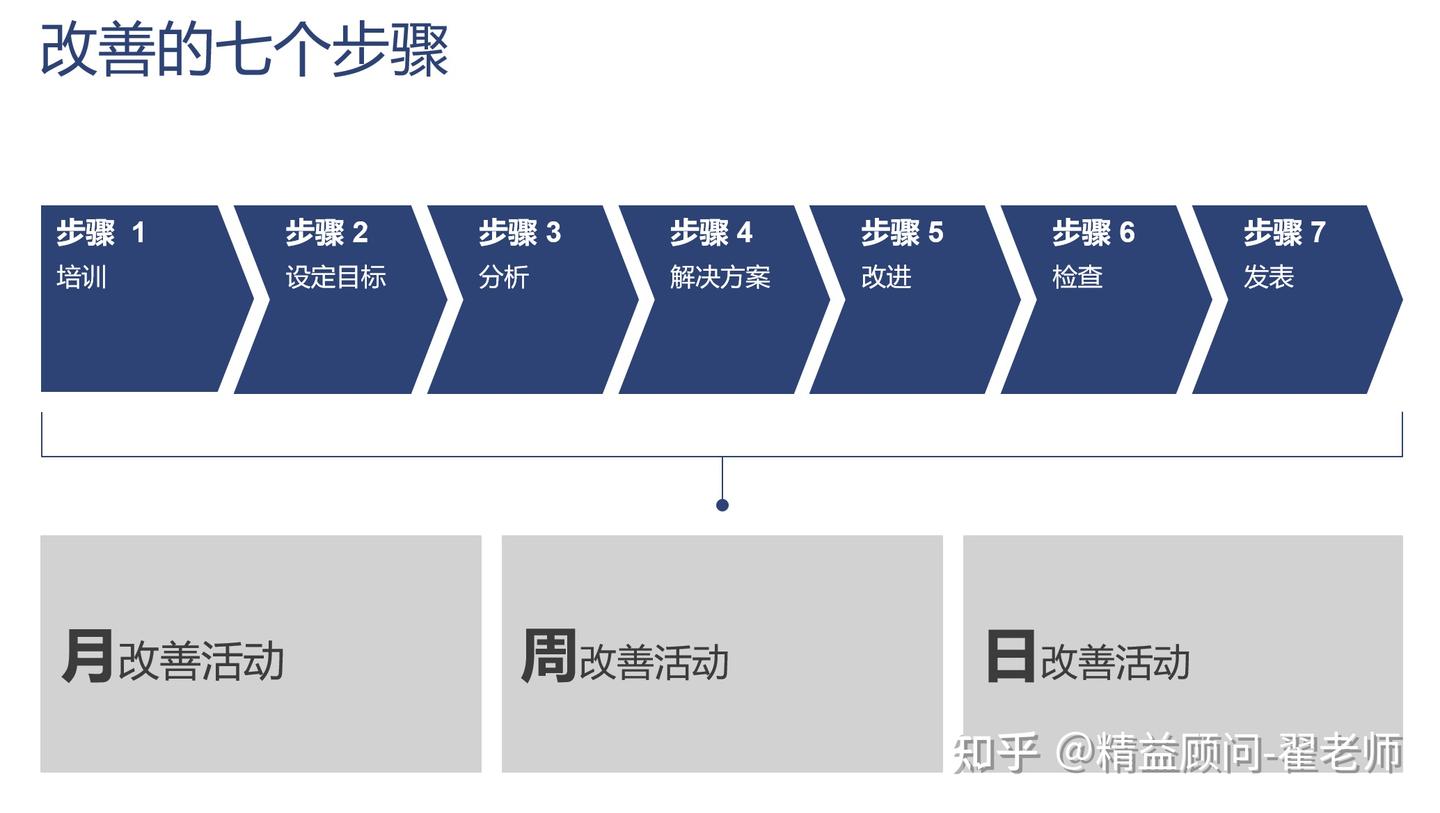
3.现场观察Go & See,培养员工
要完成仓库精益转型,需要培养有精益意识、实践、并且持续改善的员工。传统的观念过于强调工具方法的使用,而较少关注员工。
正确的精益转型是采用20%关注在精益系统工具(使用极简的精益系统比如OPEX-1588)而80%关注员工的成长。
到现场去,有组织的进行现场考场,和员工在现场、看板前讨论问题和差异,讨论解决方案。
这样经理、班组长和作业员普遍关注在现场解决问题,掌握第一手知识并且达成对问题的一致理解。每个人都有机会参与,发挥自己的专业知识。
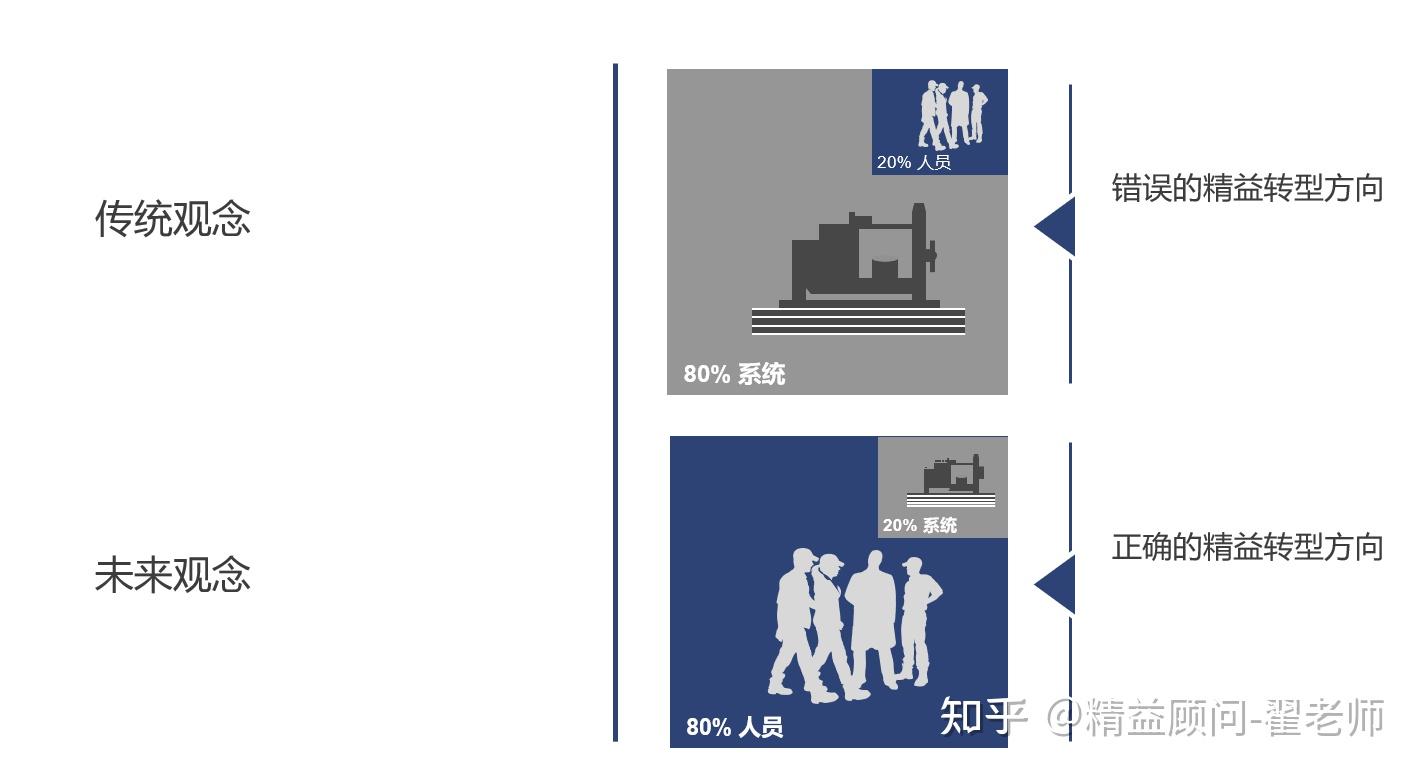
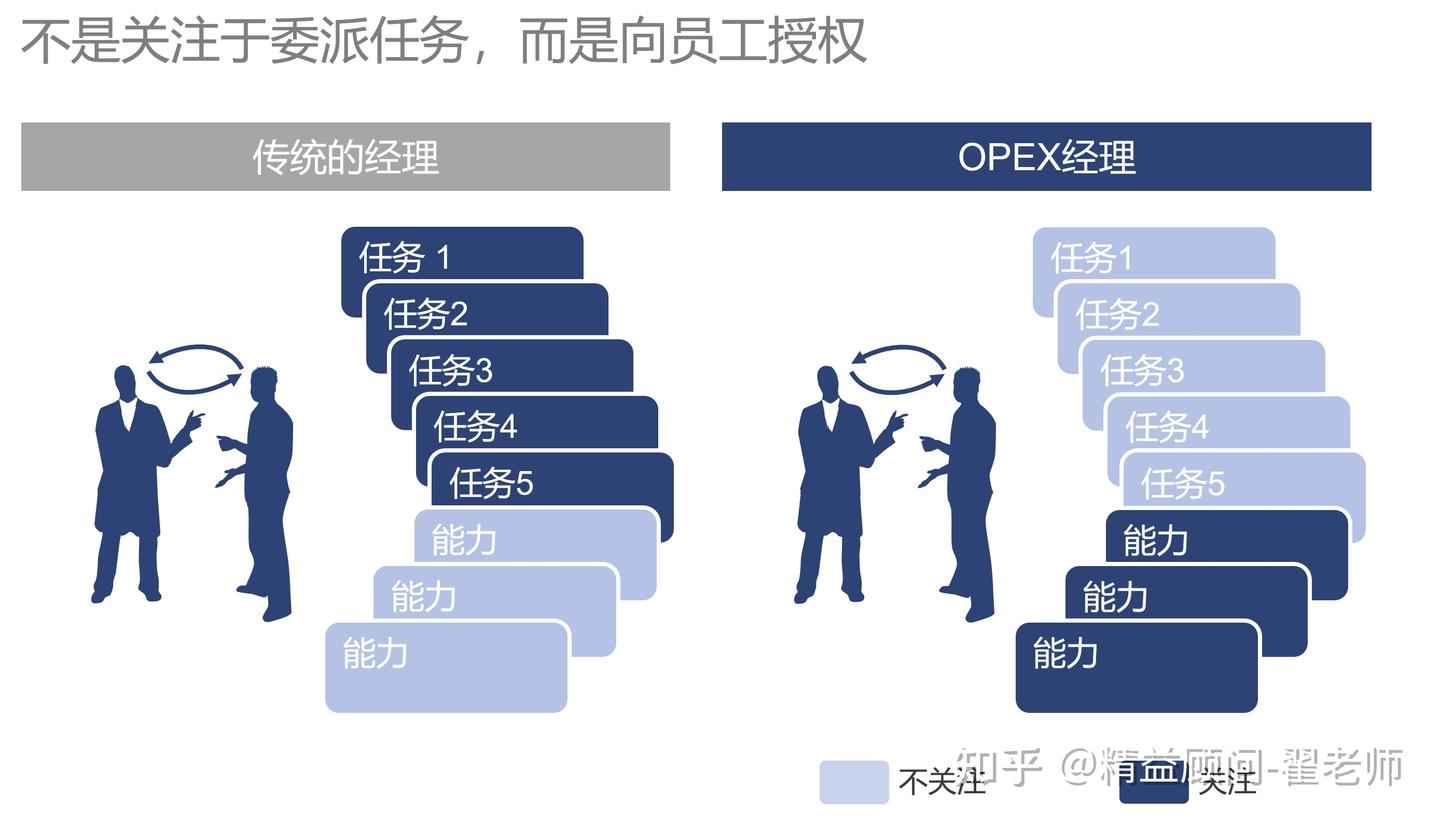
感谢您的阅读
如果您对精益仓库感兴趣,可以联系我们报名参与相关培训
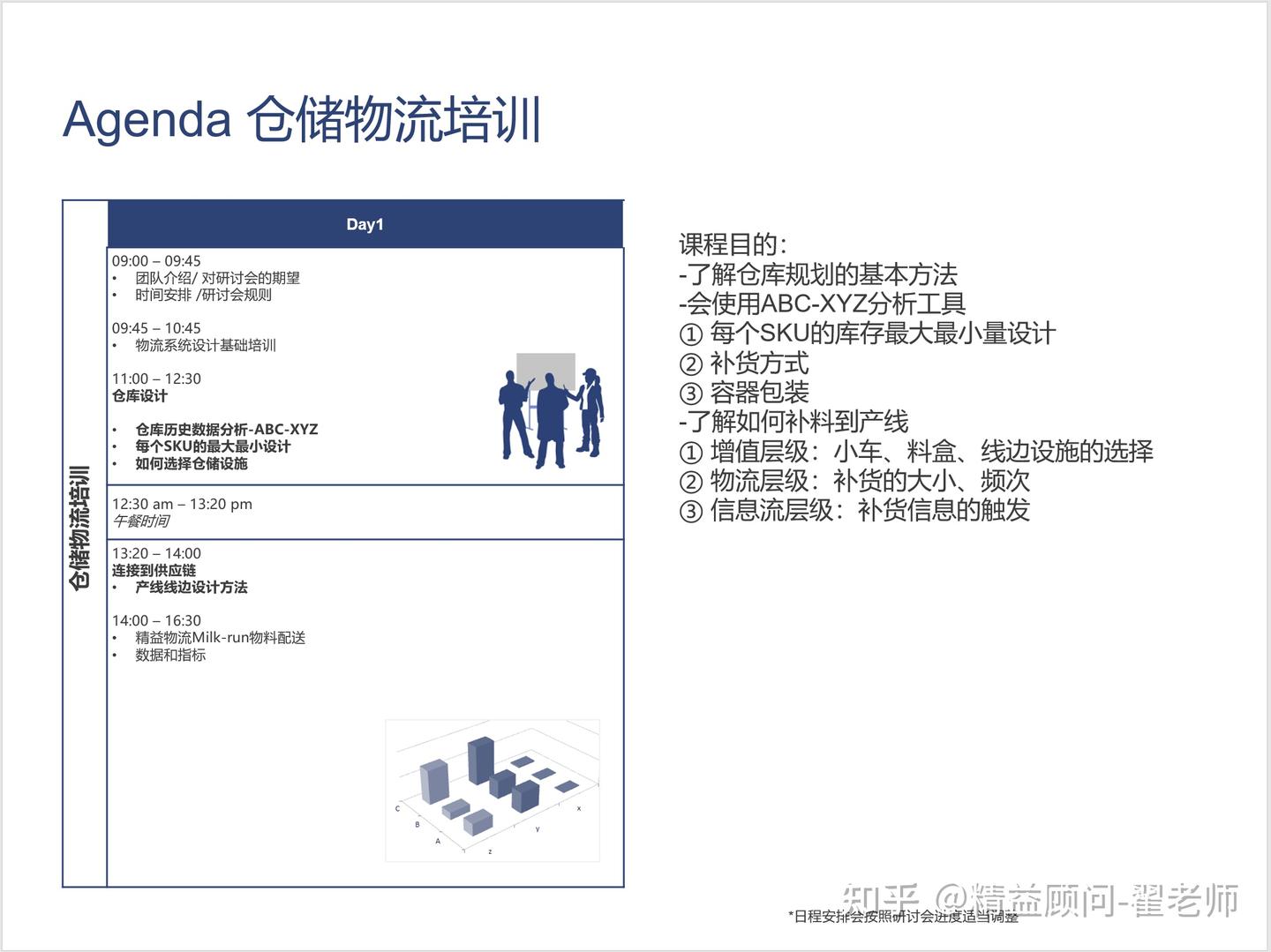
共有 0 条评论